At nearly 140,000 miles, the North American rail network has enough track to circle the earth nearly six times. It’s a vast, interconnected track system that carries 40% of intercity freight and one-third of U.S. exports.
These rails—quite literally the foundation on which so much of the American economy moves—are integral to the safety and efficiency of the network. We wanted to take a closer look at the components of rail track and some of the advanced technologies used to assess track health.
Breaking Down the Permanent Way
Rail track is also sometimes referred to as the permanent way, a historical reference to the temporary way tracks often used during construction of permanent rails. Today’s most common track structure is comprised of flat-bottom steel rails supported by timber or concrete ties, laid on a crushed stone ballast.
Top to bottom, these elements include:
Rails. Made of very high-quality steel alloy to withstand immense stress, rail segments are welded together to form a continuous line that supports railcar wheels. Continuous welded rail was first used in the U.S. in 1933, eliminating the telltale “clickety-clack” sound associated with trains. The profile of modern rail is typically that of an asymmetrical I-beam, with a head at the top connected by a thinner web to the thickest base or foot, which rests on the ties. Flanged T rail, or T-section, is the name for the flat-bottomed rail used in North America. The distance between the rails is called the gauge. U.S. railroads, along with 55% of the world’s railways, use standard or international gauge (4 ft, 8.5in).
Fasteners. The Golden Spike, driven home at Promontory, Utah in 1869 to complete the Transcontinental Railroad, is perhaps the most famous rail fastener. Spikes like it are still widely used across the North American rail network—along with base plates, themselves first introduced around 1900—to fasten rails to railroad ties and help hold rail to the correct gauge. Clips are another type of fastener for affixing rails to ties, especially in the case of concrete ties.
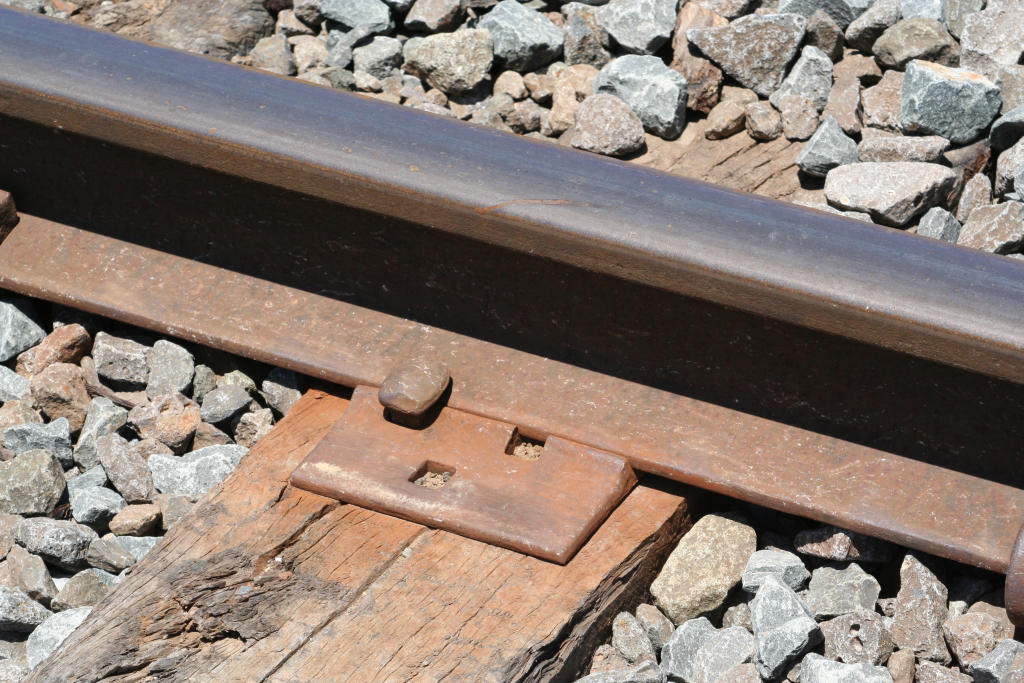
Ties (also crossties or sleepers). These are the rectangular supports connecting the steel rails. They not only help transfer a train’s load to the ballast and subgrade beneath, they also anchor the rails, keeping them upright and maintaining the correct gauge. Wood is the most common material for ties today, making up about 95% of the ties used in North America, but prestressed concrete is also widely in use. Spaced roughly 19 inches apart, there are 3,250 cross ties per mile of track.
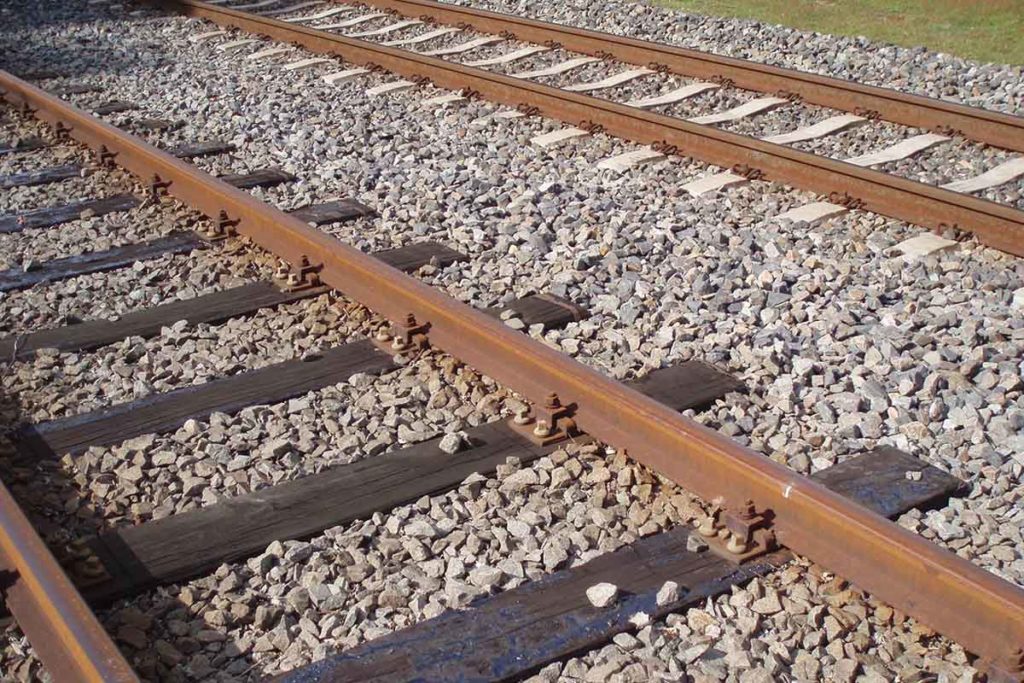
Ballast and sub-ballast. A bed of stone on which the rails are laid—packed below, between and around the ties. Ballast supports the load from the ties, rail and trains bearing down on it as well as enabling proper drainage and mitigating disruptive vegetation. To provide further support and another moisture barrier, ballast rests on another layer of sub-ballast, which itself lays atop the subgrade. The ballast should be as high as the ties, and a shoulder of about 14 inches should anchor each side to restrain lateral movement of the tracks. The stones that comprise the ballast must be irregularly shaped with sharp edges so that they interlock and guard against movement.
Inspecting the Rails
Seemingly small track flaws—imperceptible to the human eye—that can lead to accidents. That’s why railroads have developed a number of advanced technologies to inspect and monitor rail and track beds. Ground-penetrating radar, for example, helps railroads get a more complete picture of the health of ballast and detect any abnormalities, like water intrusion, which can cause erosion.
If ultrasound and smart sensors are the “eyes” monitoring track health, the rails also have “ears.” Trackside acoustic detector systems can track the energy that is transmitted from a train through the track and into the ground below—i.e. the track’s “acoustic signature.” By studying the acoustic signatures of healthy, broken and deteriorating tracks in a controlled setting, researchers are hoping to monitor tracks nationwide and detect flaws in real-time, preventing accidents before they happen.
Rail Earns Top Marks
Not only is this network vast, but it’s also America’s highest rated infrastructure system, according to the American Society of Civil Engineers. They attribute this success to private railroads’ continued “significant capital investment” totaling about $25 billion annually in recent years. Freight railroads reinvest about 40 cents of every dollar earned into their operations—about six times more than the average manufacturer.
So when you see a train passing by—hauling the goods we use every day and moving the economy forward—you may also reflect on the foundation that it all rides on: the rails, ties, fasteners and ballast that make it all possible.