Washington, DC — The U.S. freight rail industry is made up of much more than just the railroads themselves. In addition to seven Class I railroads and about 600 short lines, over a thousand additional businesses in the rail supply and contracting sectors operate in every corner of the nation to provide the components, machines, technology and services that have made the North American freight rail network the best in the world.
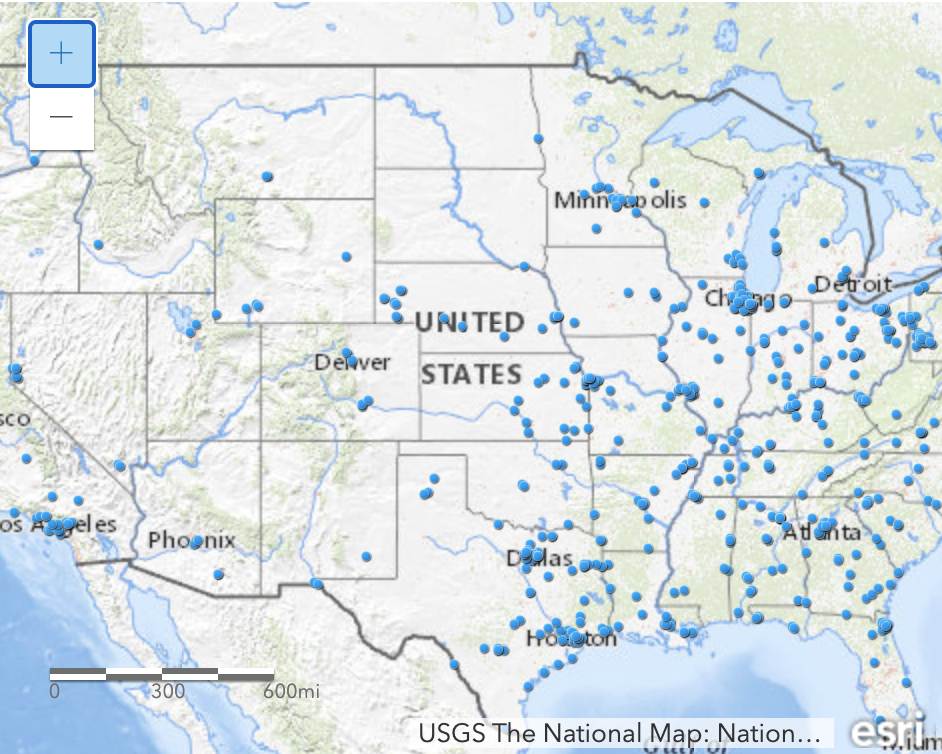
Although the COVID-19 pandemic has exposed some alarming cracks in the global supply chain, particularly in the production and distribution of ventilators, face masks, other emergency supplies and even some food products, it has also spotlighted the steadiness and reliability of one strong and unshakeable link in the chain: freight rail.
From connecting a growing nation and powering the industrial revolution to helping lift our economy out of the last great recession, railroads and their suppliers have demonstrated a remarkable ability to adapt to changing circumstances and overcome even the most daunting challenges.
That commitment to innovation is serving the nation well today as we confront the economic fallout of the pandemic, and it can be seen in every aspect of the rail supply industry—in steel mills, sawmills and concrete plants, in foundries casting freight car and locomotive components, at construction sites and track maintenance projects, in locomotive and railcar manufacturing and repair shops, and in high-tech labs and facilities designing the software, systems and equipment that continually make freight rail safer and more efficient.
Picture a nearly mile-long freight train: multiple locomotives pulling millions of tons forward on steel rails fastened to crossties secured atop a mounded track bed lined with signals and monitoring devices controlling the train’s speed and assuring its safe progress as it trails off to the horizon.
Hundreds of companies employing thousands of workers made it possible for that train to do its job. And they, in turn, supported thousands of additional jobs in their communities and in other sectors of the economy.
Teams of surveyors, engineers and construction workers designed and built the layered foundation upon which tracks were laid. Vast quantities of gravel and ballast were quarried to provide a solid foundation for the tracks. Sophisticated machinery (itself manufactured by teams of skilled workers) is deployed to monitor, and as needed, repair or replace, ballast, crossties, fasteners, rails and other track systems, and to ensure against obstructions like vegetation along the right-of-way.
Today’s locomotives are 200-ton supercomputers hauling railcars that may look a bit like the ones your grandfather could have seen, but that incorporate modern materials and technology to carry loads more safely, efficiently and productively than ever. Indeed, while freight rail remains a vast consumer of steel for virtually every aspect of rail operations and supply, the industry is as technology-focused as any other.
From ultrasound, smart sensors and radar to drones, machine learning and big data, railroads and their suppliers and contractors are using cutting-edge technology to spot issues before they become problems, better manage assets and improve an already-strong safety record.
Thousands of American workers at railroads, rail suppliers and rail contractors have kept their end of the supply chain running during this pandemic, and they are poised to provide the foundation for economic recovery.
Learn more about some of these companies via their trade associations:
National Railroad Construction and Maintenance Association
Railway Engineering Maintenance Suppliers Association
Railway Supply Institute
Railway Systems Suppliers, Inc.
Railway Tie Association